Lean Thinking is more than just a management approach; it is a mindset aimed at minimizing waste and maximizing customer value. As a software specialist or instructor, it is crucial to understand and apply the core elements of this concept. In this guide, I will explain the five fundamental principles of Lean Thinking that will help you implement successful and efficient projects.
Key Insights
The five principles of Lean Thinking are:
- Specify the optimal value-to-effort ratio from the customer's perspective.
- Define the minimal value-creating process.
- Establish responsibilities and competencies at the lowest organizational levels.
- Ensure continuous flow of results by limiting work in progress.
- Identify and eliminate errors for quality assurance.
Step-by-Step Guide
1. Specify the optimal value-to-effort ratio
The first principle of Lean Thinking urges you to think from the customer's perspective. Before starting a project, you should evaluate if it is truly necessary or if it might be a form of waste. Read the requirements and consider which tasks or projects you may be able to completely eliminate. Often, there are steps that can be combined or even omitted.
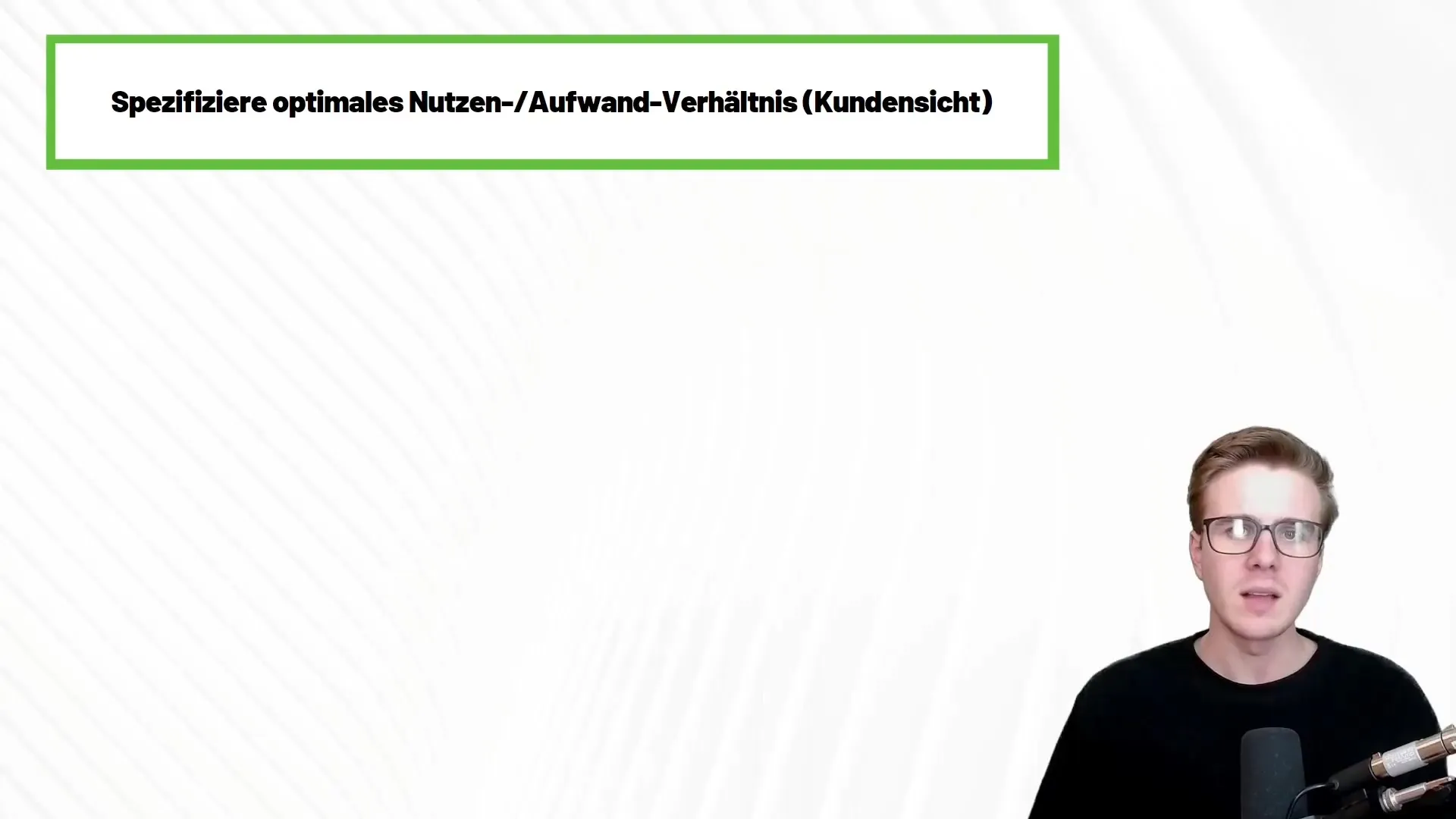
By making this selection, you reduce effort and maximize value. This means that you are able to prioritize projects that truly create added value for the customer. Pursuing unnecessary projects not only wastes resources but also valuable time.
2. Define the minimal value-creating process
The second principle revolves around designing the work process to combine the least effort with maximum value. Look for minimal processes that still offer clear customer benefits. Some tasks may get suffocated in bureaucracy, leading to a loss of flexibility.
Ensure that every step in your process adds value. If you find a task that does not provide added value to the customer, it should be reconsidered or removed from the process. Transparency and clarity are crucial here - for both you and your team.
3. Establish responsibilities and competencies at the lowest organizational level
The third principle challenges you to clearly define responsibilities. Only when everyone in the team knows exactly what they are responsible for can tasks be efficiently completed. It is important to bring responsibility as close as possible to the execution of the work.
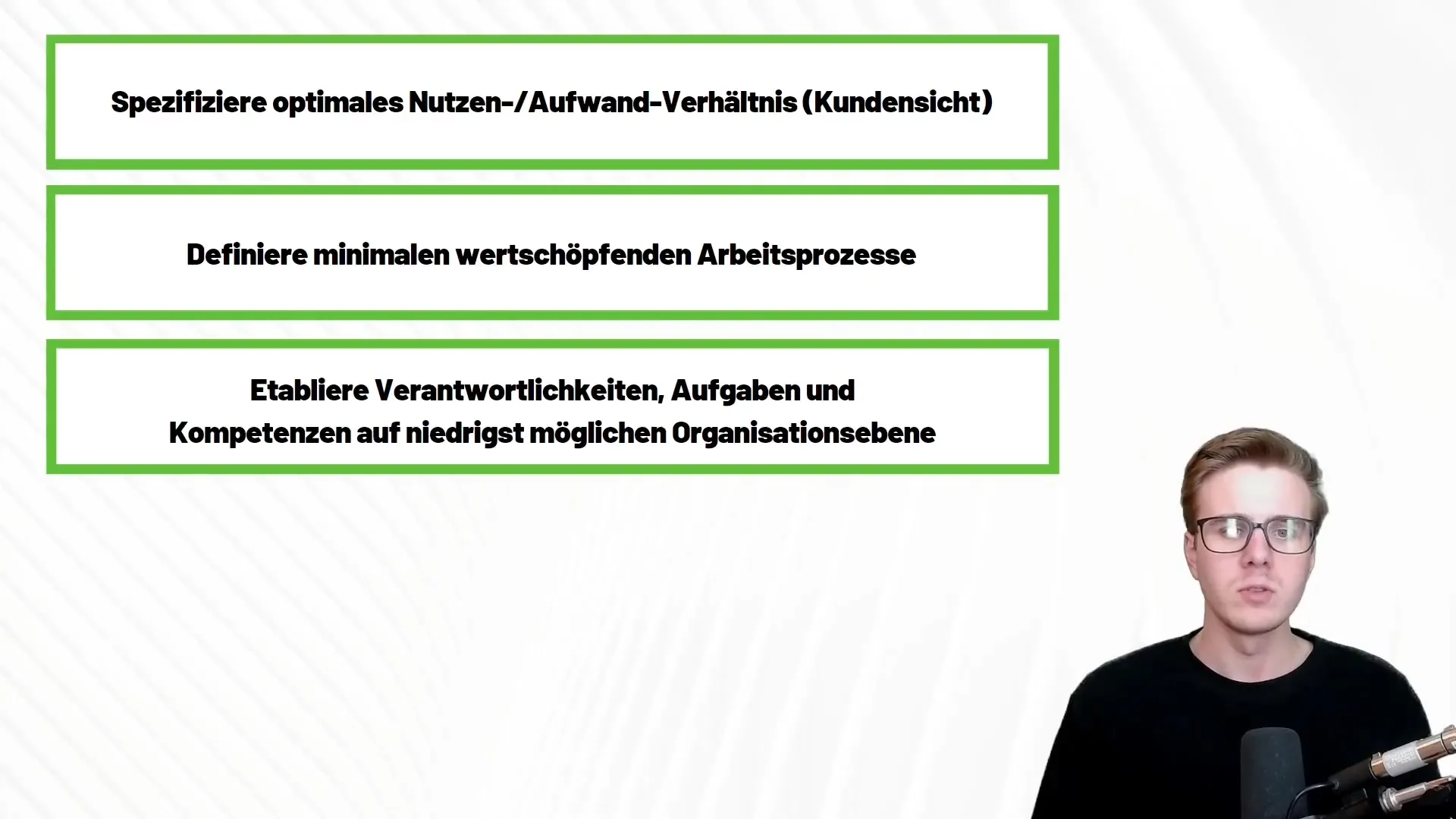
For example, instead of delegating the entire scope of responsibility to a manager, you can assign individual tasks to team members. They must then take responsibility for their projects independently. Clear task assignment motivates the employees and facilitates result control.
4. Ensure continuous flow of results
The fourth principle addresses the flow of results and the avoidance of unnecessary interruptions. Often, many tasks are started simultaneously, leading to a bottleneck. To prevent this, you should limit the number of tasks being worked on concurrently.
Tools like Kanban can help you implement this limitation. A Kanban board visualizes tasks in categories such as "To Do," "In Progress," and "Done." This way, everyone in the team can keep track and avoid unnecessary work interruptions.
5. Identify and eliminate errors
The final step is about quality assurance. To avoid errors, it is essential to identify potential issues early on. By continuously checking if everything is running smoothly, you prevent small errors from developing into major problems.
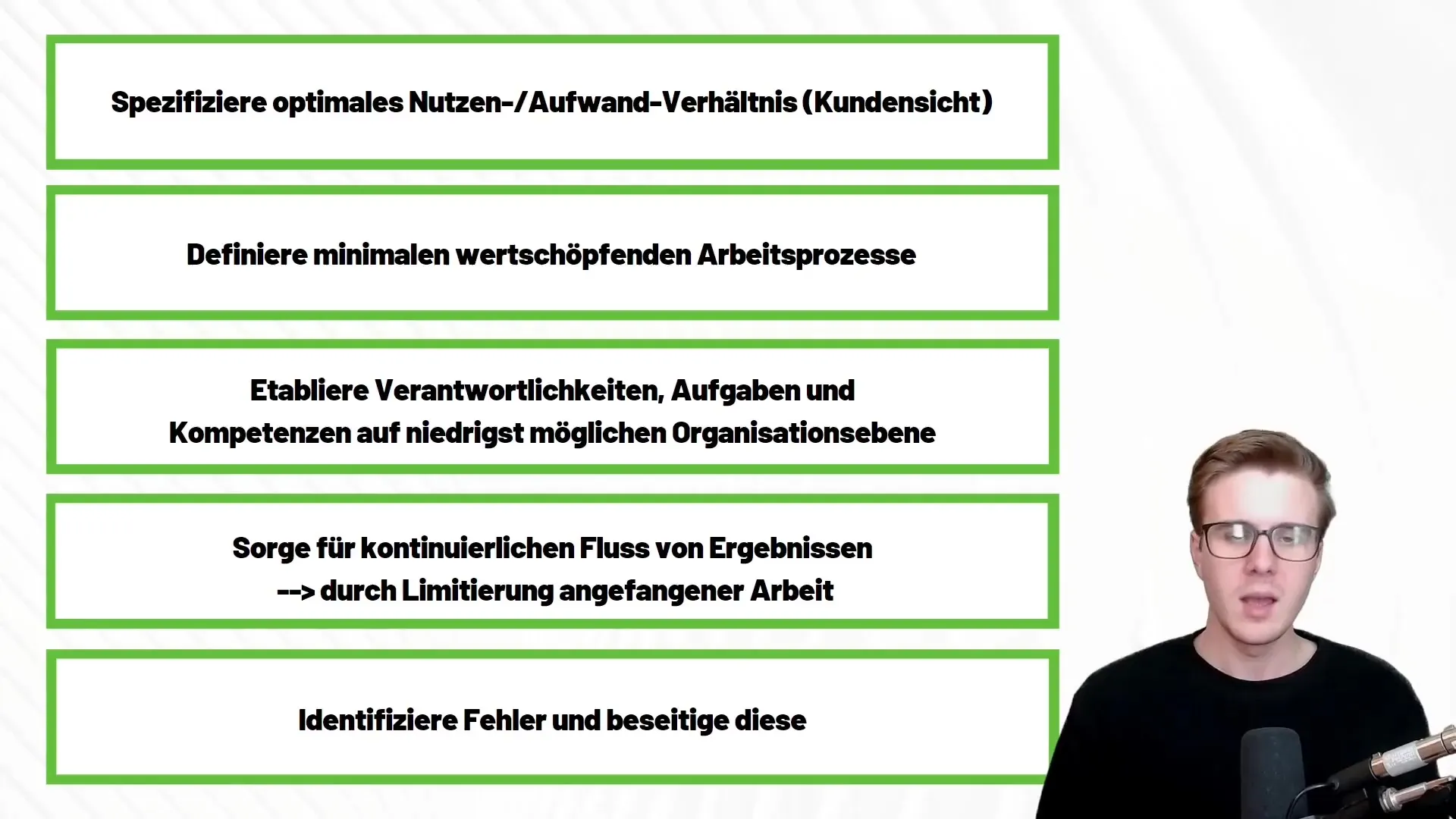
Document these checks and ensure that everyone in the team understands and applies the process. Identifying errors reduces rework effort and ultimately increases your team's efficiency.
Summary
The principles of Lean Thinking promote an efficient and customer-oriented way of working. By eliminating waste, creating clear responsibilities, and ensuring quality, you can not only increase productivity but also enhance customer satisfaction.
Frequently Asked Questions
What are the five principles of Lean Thinking?The five principles are: Value-Value Ratio, minimal value-adding process, clear responsibilities, continuous flow of outcomes, and error identification.
How can I identify waste in projects?Evaluate the necessity of each task in the project and compare it to customer expectations.
What are the benefits of Lean Thinking?Lean Thinking increases efficiency, reduces costs, and improves customer satisfaction.
How can I promote responsible action within the team?Define clear responsibilities and empower team members by giving them control over their respective tasks.
Which tools support me in implementing Lean Thinking?Tools such as Kanban and Scrum help you organize and optimize the flow of work.