Lean project management is a widely used method for increasing efficiency, helping companies to optimize their resources while increasing customer satisfaction. This article describes step 4 of the Lean principles, which deals with the transformation from Push to Pull systems. You will learn how to increase the effectiveness of your project management by working according to demand, minimizing work in progress, and focusing on customer feedback.
Main Insights
- The transition from Push to Pull mechanisms enables demand-driven production.
- Minimizing parallel tasks improves quality and reduces lead times.
- Customer feedback is crucial to adjust product development according to needs.
Step 1: Understanding the Push System
In traditional project management, as often seen in classic manufacturing processes, there is a Push system. This means that products are produced based on fixed planning cycles, regardless of actual demand. For example, a company produces ten cars monthly and offers them on the market. In this case, the produced quantity may exceed demand, leading to inventory levels and dissatisfied customers.
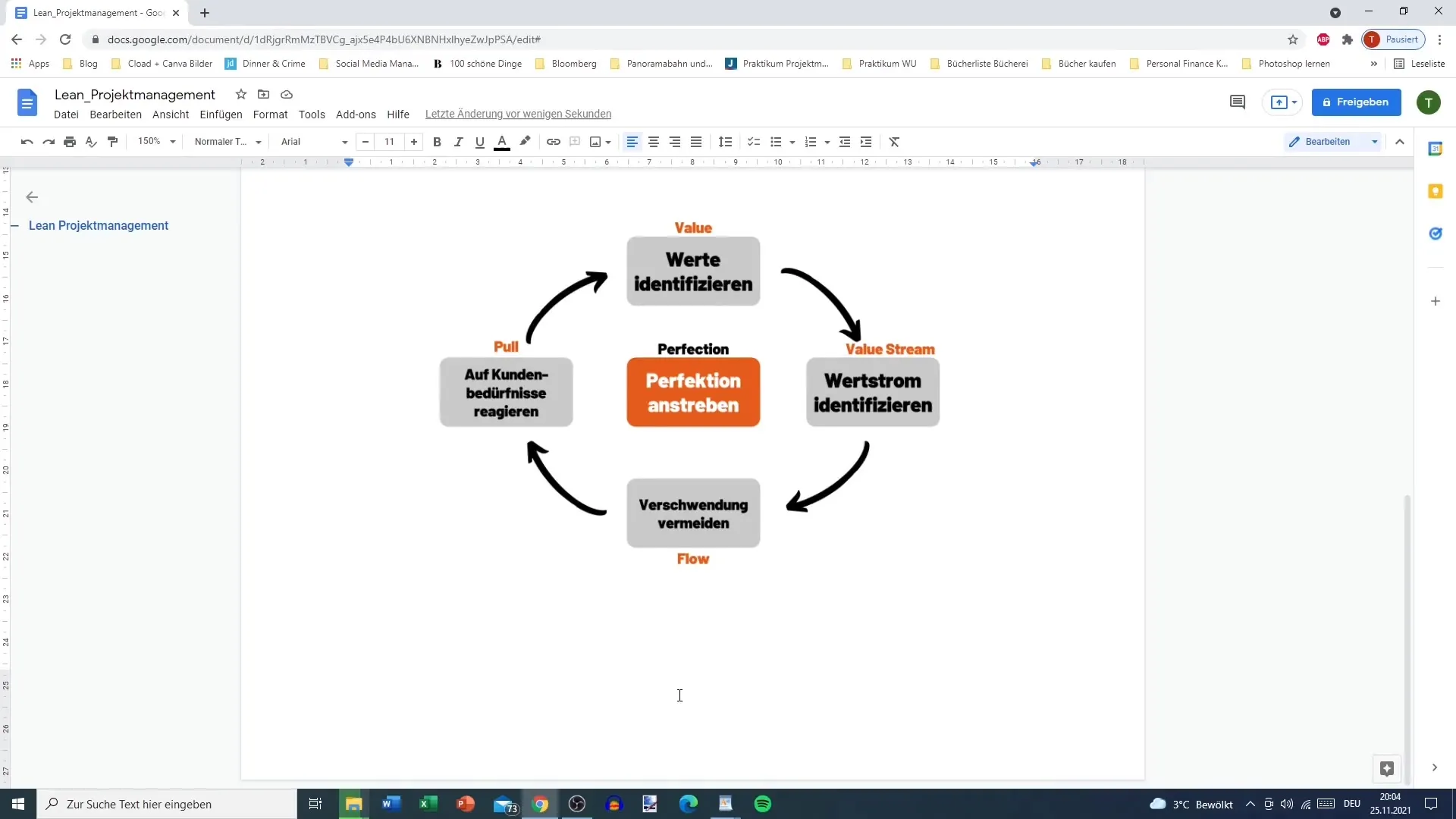
Step 2: Identifying Weaknesses in the Push System
The Push system is often ineffective as it does not address actual customer needs. Overproduction can lead to waste and high inventory costs. To meet Lean principles, a rethink is required, leading to a Pull system that aligns more with demand.
Step 3: Introducing the Pull System
The transition to a Pull system means that production starts only when there is actual demand. Customer feedback plays a crucial role. Aim to produce only the quantity of products that you can actually sell. This way, you can ensure efficient work and avoid wasting resources.
Step 4: Minimizing Work in Progress
Another key element in transitioning to a Pull system is minimizing Work in Progress (WIP). This is where Kanban comes into play. Through a Kanban board, you can visualize the progress of your tasks. Place tasks in categories like "To Do," "In Progress," and "Finished." It is important not to take on too many tasks simultaneously to avoid jeopardizing the quality of results.
Step 5: Focusing on Customer Feedback
If you have a project consisting of multiple parts, do not rush to deliver all parts immediately. Instead, it is wise to create the parts most important to the customer first. Take the time to see how the customer reacts to the initial parts. This feedback helps you make adjustments and develop the remaining parts intentionally. For example, if you are writing a thesis for a customer, you receive feedback on chapters one and two before continuing.
Step 6: Improving Quality through Focus
By focusing on the essential aspects, you can significantly improve the quality of your work. By delivering tasks that are important to your customer, you increase the likelihood of receiving positive feedback. Prioritizing quality over quantity should always be your goal. Once the prioritized parts function well, you can proceed with the rest of the project.
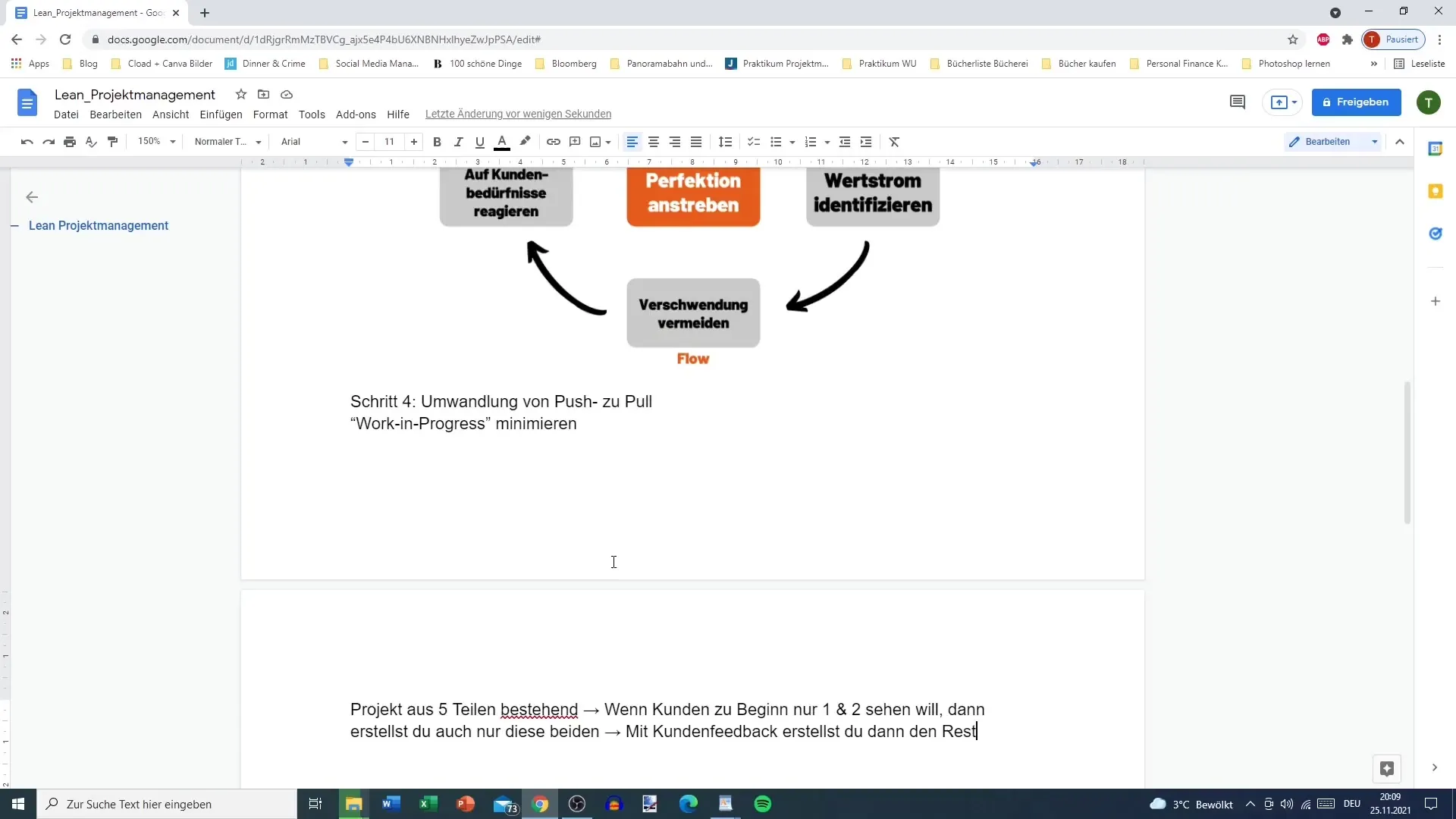
Summary
The step towards transforming Push to Pull systems in Lean project management is crucial for working more efficiently and customer-oriented. It requires a shift in production, moving away from overproduction and towards demand-driven manufacturing. By minimizing Work in Progress and utilizing customer feedback, you can not only increase the efficiency of your projects but also improve the quality of your work. Focus on what is actually needed and ensure that customer satisfaction is a top priority.
Frequently Asked Questions
How does a Pull system work?A Pull system starts production based on actual customer demand rather than a fixed plan.
Why is minimizing Work in Progress important?WIP reduction helps improve quality and efficiency by handling fewer processes simultaneously.
How can I effectively use customer feedback?Get customer feedback early to make adjustments during production and steer product development intentionally.