If you aim for a successful Lean Project Management, it is essential to consider the final step in your process. Step 5 focuses on the continuous improvement of your projects. It is not only about learning from mistakes but also about exchanging ideas within your team. In this guide, you will learn how to make effective changes by visualization and reviews to strive for perfection.
Key Insights
- Continuous improvement is a key element of Lean Project Management.
- Exchanging best practices and experiences within the team is crucial.
- Visualization and shared reviews enhance learning from mistakes.
- Perfection is only achieved when all team members are involved in the process.
Step-by-Step Guide
Step 1: Understand the principle of continuous improvement
Before you start implementing, you should thoroughly understand the concept of continuous improvement. It is an ongoing process that aims to constantly optimize your workflows and products. This is done through analyzing past projects and learning from successes and failures.
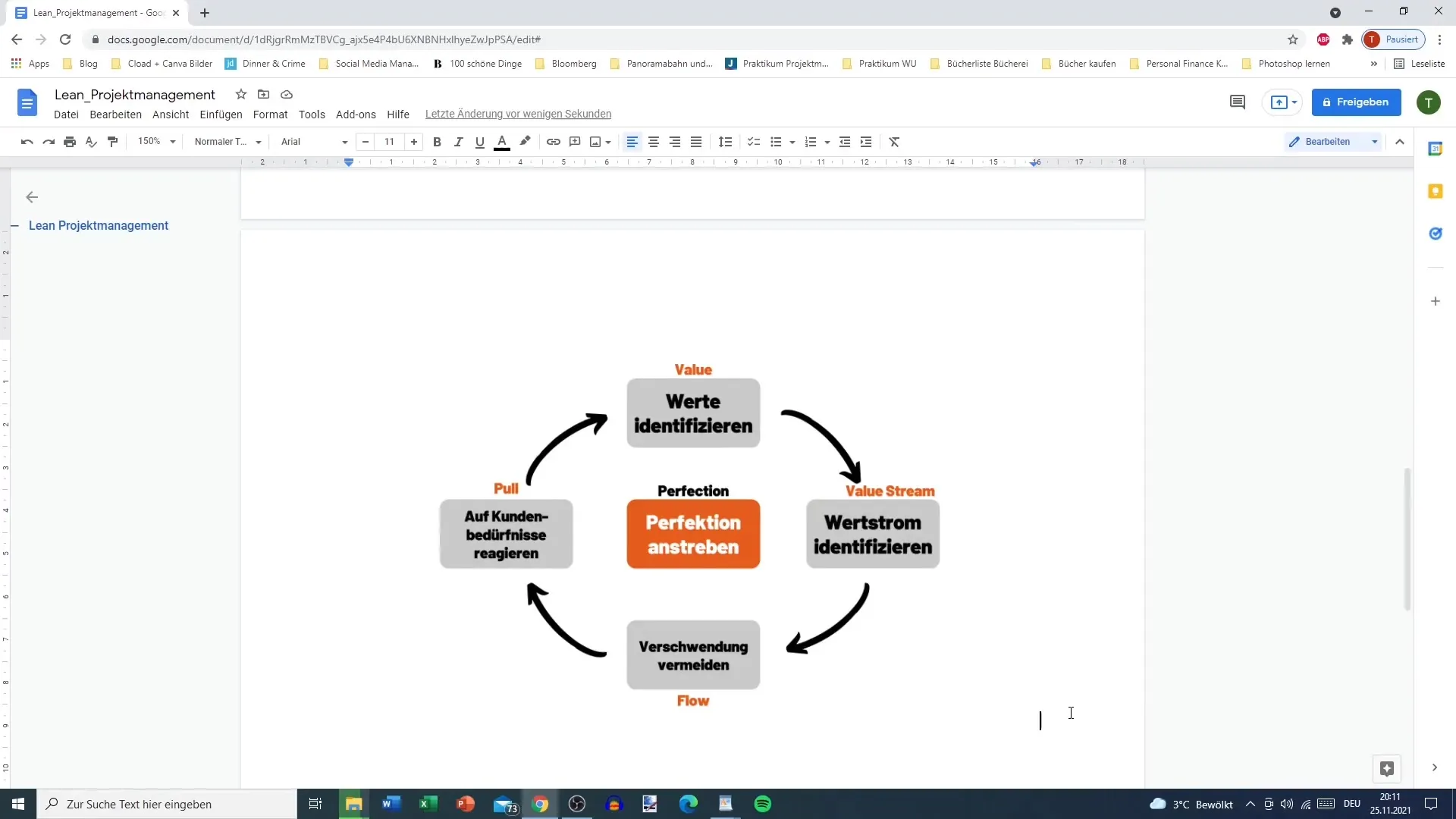
Step 2: Visualizations are key
To effectively shape continuous improvement, it is important to visualize all relevant information. Use tools like diagrams and graphics to clearly represent your best practices as well as areas needing improvement. Visualizations help not only you but also your team to gain a better overview and identify necessary changes.
Step 3: Conduct regular reviews
A central aspect of Lean Project Management is holding reviews. Sit down with your team and discuss current projects. Such an exchange should take place at least once a month. These meetings help not only to identify past errors but also to celebrate successes.
Step 4: Involve team members
It is crucial to actively involve your team members in the improvement process. Progress can only be made if all participants understand the need for changes and are willing to implement them. Emphasize the importance of every team member being able to voice their opinion and being open to criticism and suggestions.
Step 5: Create a culture of learning
To successfully implement continuous improvement, it is important to foster a culture of learning. This culture should be characterized by appreciation and support. Motivated employees who see themselves as part of the process are willing to share their experiences and contribute suggestions for improvements.
Step 6: Set goals for the future
Define clear goals that you and your team want to achieve with your improvement measures. These goals should be both short-term and long-term to promote sustainable development. Regularly reviewing your progress helps to adjust the course and ensure that your efforts are heading in the right direction.
Step 7: Learn from the past
Memories of failed projects are valuable learning resources. Regularly go through past projects and analyze them together as a team. This reflection allows everyone to learn from mistakes and develop strategies to avoid them in the future.
Step 8: Gather feedback
To support continuous improvement, it is important to gather feedback from various sources. This can be done through surveys, conversations, or anonymous feedback. Seeking opinions brings new perspectives into the process and fosters an open climate of improvement.
Summary
The final step in Lean Project Management emphasizes the importance of continuous improvement. By effective visualization, regular reviews, and involving all team members, you can steadily enhance the performance of your project. A culture of learning and the goal of always getting better are crucial for the long-term success of your project.
Frequently Asked Questions
How often should I conduct reviews?At least once a month to discuss and analyze current projects.
Why are visualizations important?They help communicate information clearly and identify areas for improvement.
How can I actively involve my employees?Create an open climate where opinions and suggestions are welcome, and appreciation is shown.
How do I deal with errors from past projects?Analyze them systematically as a team and learn from the mistakes for future projects.